BMW 3D prints new thumbs for factory workers
German car manufacturer put new technology in place to reduce strain on manufacturing-line workers' hands
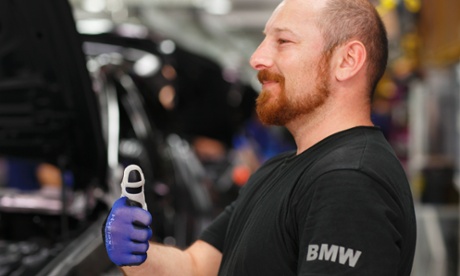
German car manufacturer BMW has turned to 3D printing to physically augment its car-plant workers, giving them stronger, augmented thumbs.
The 3D-printed apparel acts like support brackets for the workers’ thumbs, reducing strain and helping them to fit certain parts into the cars more easily.
Each "thumb" is created as a custom orthotic device using a portable 3D camera, which captures the unique size and shape of each line-worker’s thumb.
Lasers, plastic, scanners and thumbs
The scan is then used to build up a thumb guard made of a semi-flexible thermoplastic polyurethane plastic – a hybrid material mixture of hard plastic and soft silicone – which is create by a 3D-printing technique called selective laser sintering.
A laser is used to fuse plastic powder into layers, building up the structure one thin slice at a time until the full 3D structure is created.
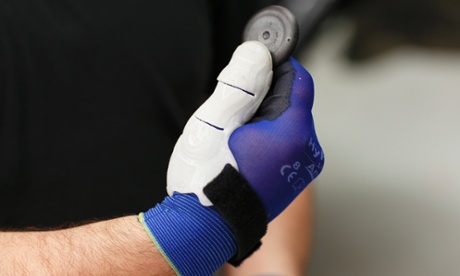
The finished thumb guard flexes in a closed position. But because the structure is perfectly fitted to the wearer’s thumb the pieces lock into place when the digit is raised into a thumbs-up position.
Iron Man for the thumb
The locked splint resists strain and spreads the load of pushing something like a stiff rubber plug into holes in the car’s chassis – something that was causing pain and strain for production-line workers.
After small trials in the company’s Munich vehicle assembly plant yielded “very positive” feedback from workers, BMW is now looking to roll this and other schemes using custom built 3D-printed apparel to help production and prevent pain and injury.
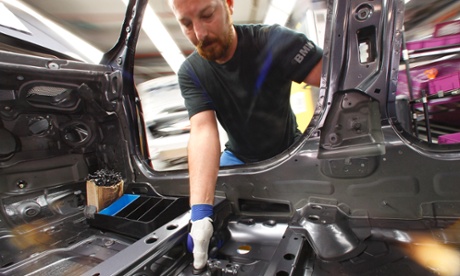
3D printing for the last 25 years
BMW has been using 3D printing techniques as part of its prototyping of parts and cars since 1989 with around 100,000 pieces created a year using a variety of different techniques at the Rapid Technology Centre in Munich.
This is not the first ergonomic aid BMW has created used 3D printing. The German automotive company created customised wheelchair seats for the British paralympic basketball team in 2012 using similar methods.
The creation of the new thumb cots is part of a project at the Department of Ergonomics at the Technical University of Munich.
Other projects have used 3D printing to replace limbs with cheap, adaptable prosthetics, along with a large number of other interesting objects and creations that were not possible using traditional manufacturing methods.
沒有留言:
張貼留言